The Basics Of Vapor Retarders In Metal Buildings: The What, Why and Where
July 16, 2020
The WHAT
What Is A Vapor Retarder?
A vapor retarder is a material designed to limit the amount of moisture in the air from traveling through it. The effectiveness of a vapor retarder is measured in terms of the permeance of the material. The Permeance is defined as the rate of water vapor transmission through a material in a given amount of time per unit area. Most of us in the industry know this as the “perm” rating. The lower the perm rating, the less moisture that is allowed to pass through the material. The 2015 International Building Code identifies three classes of vapor retarders per ASTM E96 as:
- Class I: 0.1 perm or less
- Class II: greater than 0.1 per to less than or equal to 1.0 perm
- Class III: greater than 1.0 perm to less than or equal to 10 perm
With the exception of Plain Vinyl (Class II), the vast majority of facings used within the Metal Building Industry have a perm rating of less than 0.1 (Class I).
Per the National Building Code – 2019 Alberta Edition Volume 1, Section 1.4.2.1 Defined Terms, a Vapour barrier means the elements installed to control the diffusion of water vapour.
The WHY
Why Would A Vapor Barrier Be Needed?
The primary reason to have a vapor retarder is to help control condensation within a building system. ASTM E241-90 states “observations have shown that apart from structural errors, a high percent of building construction problems are associated with water.”
Depending on time of year and the climate zone of the building’s location, the amount of moisture in the air can vary. Other factors that can contribute to the moisture content in the air are rain, snow, ground water and concrete. When metal is exposed to moisture for extended periods of time, oxidation can occur, which can weaken and shorten the life expectancy of a metal building. The best way to help protect a metal building is to substantially reduce or eliminate the potential of moisture.
The WHERE
Where Is A Vapor Retarder Used?
Again, depending on the design, intended building use, location (climate zone) and codes, a vapor retarder will be used in conjunction with fiberglass insulation as part of the metal building envelope.
However, there are basically two general configurations regarding vapor retarder placement within the metal building envelope.
1. The vapor retarder exposed to the interior of the building and covering the fiberglass insulation. This configuration can be seen in the figure below.
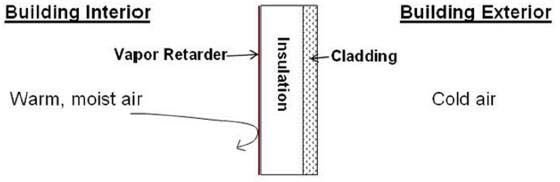
In this instance, the exposed interior vapor retarder will inhibit the moisture from the warmer, interior air from passing through the facing and insulation to the metal cladding. If the vapor retarder were not present, the moisture from the interior air could condensate on the cold metal cladding, thus creating the formation of water droplets that could saturate the insulation and corrode the metal.
2. The vapor retarder installed to the exterior side of the fiberglass insulation and the interior side of the metal cladding as shown below. In this case, a perforated facing typically covers the interior side of the insulation.
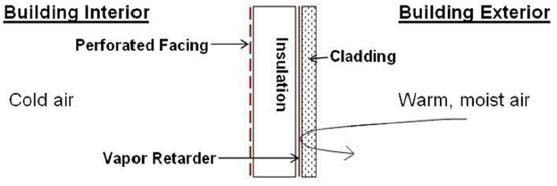
This configuration is typical in applications in high humidity areas. In this case, any unwanted moisture that passes from the outside air and through the metal cladding and insulation can permeate into the building’s interior. The unwanted moisture can then be removed via the HVAC system within the building.
In both configurations 1 and 2, the vapor retarder can be purchased and installed directly to walls and ceilings of the building, or fiberglass Metal Building Insulation can be purchased with a vapor retarder attached (i.e. Laminated or Faced Metal Building Insulation).
As mentioned previously, the location, orientation and perm rating of vapor retarder in the design and construction of metal buildings should be reviewed by local architects and building inspectors. This is mainly due to the different building dynamics, systems and environments in each applicable case. The orientation of vapor retarders to the exterior of the building is discussed in the 1993 ASHRAE Handbook– Fundamentals, pages 21.11 – 21.13, as well as in the National Building Code – 2019 Alberta Edition Volume 1, Section 5.5.
Other references used for information within this article are:
- Lamtec Technical Bulletin #2
- Lamtec Technical Bulletin #9
- Lamtec Technical Bulletin #14
- Lamtec Technical Bulletin #15